Restoring An Old Gun From The Ground Up (literally)
I like a challenge and to try things I haven’t done before and this project is a real challenge. Many years ago this old shotgun was wrapped in burlap and buried in the ground and remained there for 7 years. As you would expect, when the gun was unearthed the wood was gone and the metal is very corroded. This particular gun then remained in a state of disrepair for many years afterwards. I was contacted by the owners asking if I could restore this weapon since he was a fan of my prior restorations.
The shotgun is a Enders Royal Western 16 Ga. Break action. The top of the barrel is stamped with the following.
“Electro Steel Choke Bored gun patented August 12 1913”
Web searches state that the shotgun was made by Crescent Arms Co., which was associated with H & D Folsom Co. until the demise of both in the early 1930's.
The Enders Royal single shot scattergun was manufactured in an era when it was considered an inexpensive farm tool.
Enders Royal was a "Trade" name used by the Crescent-Davis Firearms Company on shotguns made for the Shapleigh Hardware Company of St. Louis, Missouri. Crescent merged with Davis in 1920, and was bought out by the Savage Firearms Company in 1930. This gun was made somewhere in the 1918 - 1929 timeframe.
I was asked if I could restore the old gun into service. This is not to be a show piece since the original gun was a hardware store “farmers” tool. The goal here is to return the shotgun to usable service to be fired and then perhaps hang on a wall in restored condition. It has sentimental value more than anything. Its not meant to be a trap gun or a shotgun that will see a lot of use
I have restored a many firearms in the past but the guns always had a stock or I could at least purchase a replacement stock. That is not the case with this old shotgun. Weeks of searching for a replacement stock online got me nowhere. Emails to custom stock makers were also dead ends. I have never made a stock before but that’s about to change. I have only modest tools and don’t plan to purchase tools for this project.
Here is the shotgun as I received it.
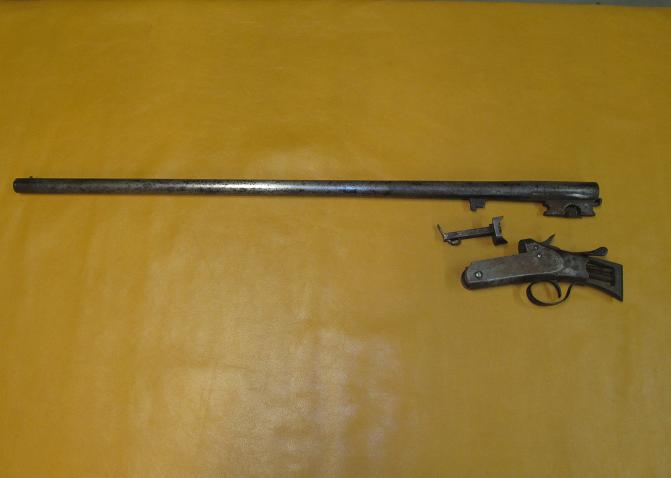
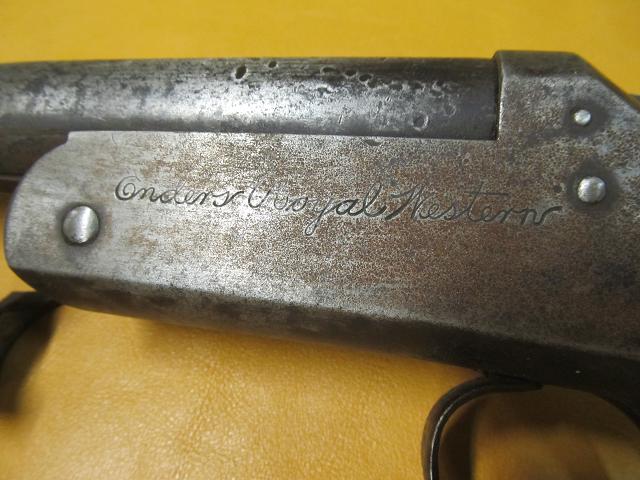
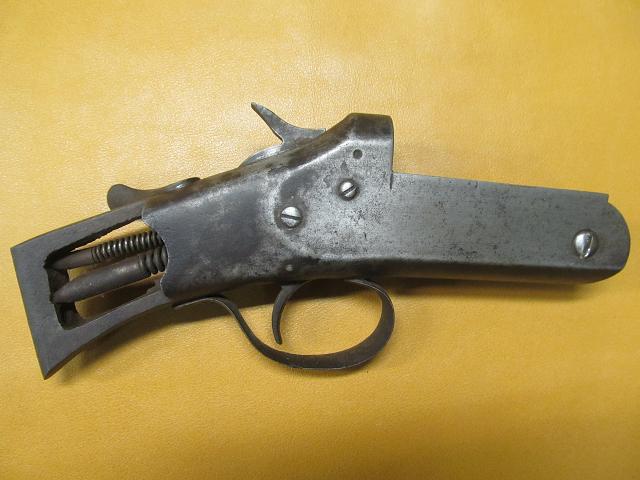
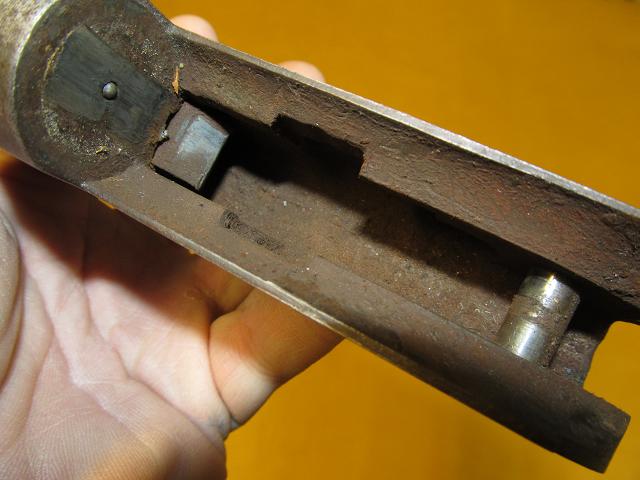
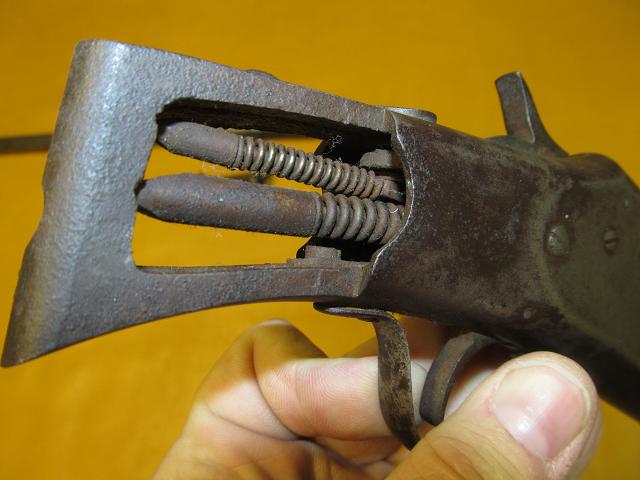
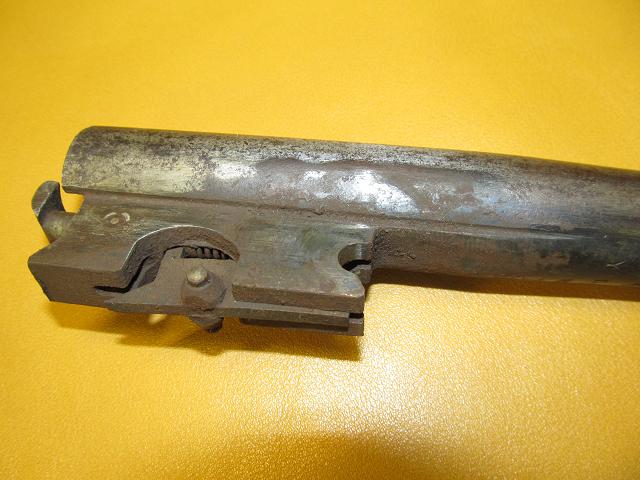
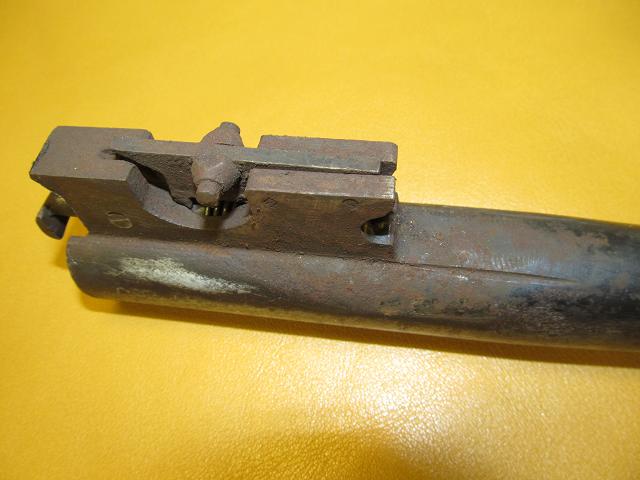
Below is the spring mechanism that will go into the forearm stock. The forearm grip of a break action shotgun is removable as the first step in taking the gun apart. Once the fore-grip is removed, the barrel can be removed from the receiver.
My search for a replacement stock got me nowhere but I was able to find a picture of the old gun from an online auction site that sold the gun years ago. This is all I have to go by in regards to making a stock. It’s not much but it’s a start.
It appears that the barrel was blued but the receiver and trigger guard were plated in a metallic finish. While I can cold blue I will need to come up with an alternative for the receiver (or just blue it along with all the other metal parts).
I used that screen image to create a full scale sketch of the stock I hoped to make but again I have never made a gun stock. If I can’t make a stock there is no point in restoring all the metal so stock making is where I have to start.
A few years ago my brother cut down a black walnut tree and had it sawn into dimensional lumber. It’s been sitting in his shed for a few years. He gave me a piece that measures 4" x 8" x 7 feet. Somewhere in that twisted, cracked, checked, knotted and bird crap covered piece of wood, there are two pieces of a gun stock. That walnut beam is solid and heavy and it looks like there are blonde streaks running through it. I grabbed the hand saw and loped off a chunk for the fore grip stock.
The foregrip is pretty small. I found a good looking piece after cutting it on my table saw.
I have to pocket out for the spring latch that holds the stock to the gun.
I plan on doing as much of this project old school as I can. Chisels, rasps, saws, planes, shaves, carving tools, sanding blocks, etc. I don’t have a milling machine or router. I have a drill press but that's not much good here. So it begins. For the smaller features I used an exacto chisel.
I have to make the barrel fit the length of the block. The table saw is the best choice here.
To get rid of the ridges left by the saw blade I employed the handle from my shop broom and some sandpaper. I can add broom handle to the list of hand tools for the project. It worked just fine. Where the barrel meets the receiver it flares out a bit. I laid the barrel on the stock and scribed lines and used carving tools.
I would coat the barrel with pencil carbon and lay it in the stock and give it a twist. It left marks telling me where it made contact and where I needed to take away more wood.
Then some profile cuts and a hole for the screw that mounts the spring mechanism.
Then a whole lot of sanding and a counter-bore so the screw head sit below the surface.
After the work was mostly complete (final sanding) those blonde streaks showed up.
I don’t know if they add character or are ugly. Too soon to tell but I don’t feel like starting over since any other piece might have more blonde streaks in it as well. So far so good. No screw ups and no injuries.
The next step is to make sure the spring mechanism fits and the spring can move freely. The spring mechanism is held by a single screw. That screw was missing so I need to replace it. No doubt the original screw was black in color (blued) My local hardware store does not carry machine screws in any color other than shiny zinc plated. No worries. I polished off all the plating by spinning the screw in a drill and using 800 grit sandpaper then blued the screw head with the last remains of my bottle of Brownells Dicropan cold bluing and then gave it a light oil coating. I have had good results with Dicropan in the past so I need to replenish my supply for the rest of the parts of this shotgun.
Here are the before and after pictures of the screw. After polishing
After bluing.
To dress up the appearance of the screw (since it has to be seen for removal) and to protect the wood from being crushed by the spinning of the screw head into the wood I drilled the hole slightly larger than the head and will use a cup and fiber washer from the hardware store to spread out the load on the wood. I like the look and the fit seems good.
The spring mechanism fits well in the chiseled out area.
Now for the real test, does it fit and does it work??
The broom handle gets an A+ for fit.
Im not sure what finish the original stock had back in the 1920’s but I can be sure it didn’t come out of a rattle can. It may have been some sort of shellac or varnish but more likely was been boiled linseed oil as that was a typical gun stock finish (and still is for high end guns) It may have also been tung oil which is still used as a gun stock finish. Both Boiled lindseed and Tung oil are available at the local hardware store and both are drying oils (unlike mineral oil that would be used on cutting boards). The major difference in tung and boiled linseed oils is the dry time. Linseed oil means 6 to 10 days between coats since its very slow drying. If I want to apply 6 to 8 coats, that would means months worth of waiting. Tung oil can be reapplied after 24 hours meaning the 8 coats will cost me just over a week so I will go with the tung oil. I added a makeshift handle to hold onto while doing the final sanding with 800 grit and for applying the tung oil.
A hand rubbed finish means just that. The brush I will use to apply the tung oil is one of a set of ten that I got from my parents on my first birthday and despite projects like this (and growing up on a farm) I still have all ten of those brushes after 50 years. Here is the foregrip after the first of many coats. Not very impressive but that first coat was sucked in nice and deep by the thirsty wood and will lay down the base for the next 7 coats. Each coat will add a level of protection and gloss/shean.
One stock piece (sort of) complete. Time to start the butt stock. In the meantime I placed an order for some needed supplies for this project. These supplies are about 10 times the cost of the original shotgun when new.
I don’t have the tools (tall drill press) to pull off drilling a 16 inch deep hole through the entire butt stock for the mounting bolt that attaches the stock to the receiver so I need an alternate way to make a butt stock with a way to access the bolt for assembly.
The long bolt that holds the gun to the stock was not with the gun so I need a replacement. My hardware store did not carry a 5/16 fine thread machine screw as long as I need note with a straight slotted head for a screwdriver so I bought a bolt and slotted it myself.
It dawned on me while looking at some of the knives I’ve made and the bows I have made that there might be a way to make the stock that fits with the simple tools I have and things I have built in the past. Then I got to thinking about the trend in gun stocks being laminated from many layers of wood and epoxy (some seem to have more epoxy than wood). I will make a laminated stock with only two laminations. I will split the stock in half to pocket out for the long bolt then epoxy it back together.
Today’s epoxies are very strong and I have had great luck with them for knife handles and laminated bows I have built so I have no concerns that it will bond this walnut with strength matching a solid piece of wood.
Back to the Walnut beam. This looks like a good section. Yes that is dried blood on the beam. I hauled the beam home with my gun season buck in the back of my truck and blood got on the beam.
Here is a view of the end grain. Perhaps there wont be any blond streaks in this piece. I am at the complete opposite end from where I got the forearm grip.
I cleaned up the beam and then sent it through my table saw creating a book end, matched set of slabs with one slab being slightly thicker than the other which will make sense later on. I dont have a planer but I was able to sand the two surfaces down to get rid of the saw marks so that the glue line will be very thin and clean.
I used the table saw to cut a slot for the screw and another for the washer under the head of the bolt. I had to repeat it for both halves. Then I used a chisel to square up where the curve of the blade did not cut away the wood.
Then I needed to remove the wood where the shoulder of the receiver will fit. That part is about a ½ thick. This will leave a square shoulder but the back of the receiver is a full round.
This is where is gets rough. There are timing issues. The new radius at the back must match on each side. That’s easy enough but at the exact time the wood and metal meet at the back, the wood and metal at the end of the stock must also match or there will be a gap at one end or the other. This has to be addressed on each half. I can rough out the profile with a coping saw but then the detail work will come from chisels, knives and sandpaper.
To make things more difficult, the coutour at the receiver end is not a square cut. Its beveled backwards. Who came up with this design????? Its like they said, “lets make this as difficult as possible so that in 100 years the guy making a replacement stock will have to pull out his hair to duplicate this work”.
The hand saw gets me close and then carving tools and sandpaper take it the rest of the way.
Both halves of the receiver joint are complete then the halves are rough cut to the shape I need.
For added strength and for alignment I will use 9 hardened steel pins hidden within the stock. This will add to the epoxies shear and tensile strength but it also ensures the flat for the washer on both halves lines up during the slippery clamping process
This slow cure epoxy has a 3,000 PSI tensile rating, can be drilled and tapped, is waterproof and heat resistant and does not shrink. It also has a good wetting property (since its slow cure). Their data sheet shows a 1,345 PSI shear strength on maple to maple. As I have stated I have used this many times in the past on wood laminations with incredible success.
Epoxy likes rough surfaces so before I applied the epoxy I roughed up both halves with a hacksaw blade by bending a blade into a “u” shape and raking the teeth across the wood. Its important to coat both surfaces for the best adhesion. It uses more glue (which oozes out during clamping) but you can be sure you wont have any dry spots starved of epoxy.
Light clamping pressure is all that is needed to ensure you don’t squeeze out the epoxy. After 24 hours the epoxy will be fully cured then it will be one solid piece. I used flattened stick to make sure to scrape out the epoxy the oozed into the channel for the bolt. While the epoxy was still curing I lowered the large washer down into the hole so it stays with the stock. Only the lock washer will be removed with the bolt during disassembly in the future.
The Brown truck made a delivery to the house .
The epoxy is cured and the stock is unclamped and cleaned up to the rough outline.
But the stock is the same thickness from back to front.
All the stocks on the guns I own are tapered from the butt end to the grip so I will do that next.
I set a depth on each side so I know when I went deep enough. Then lots of chiseling and sanding to remove all the wood.
Then I used the butt plate as a guide for shaping. Remember I made one slab of wood thicker than the other. That was so I could bias the screw holes to one side rather than right on the glue joint. Now its time to remove all the corners and round the stock.
This was the wrong tool for the job.
This was a better choice to keep the comb straight. It allowed me to remove a lot of material very quickly.
After a lot of sanding to the outline of the butt plate, one corner is done, three more to go.
Fast forward and all the corners are finished..
The sanding left a radius at the base of the grip.
Time to break out the chisel again. And more sanding to finish with a clean and sharp line.
The original gun most likely had only a black butt plate. While that’s fine and all, I hoped to dress it up a bit more so I cut up one of my flexible cutting boards and the divider out of a three ring binder to add a bit more style. (nothing but the best for this job. plus the guy in the cube next to me will never know those dividers are missing)
I think it adds a bit of class to the look without adding any cost.
The step that I failed to show was rounding the bottom of the grip. This stock wont have a flat grip nor a plastic grip cap so I rounded it off. You can see that rounding in the pic above.
The next steps are to point and flute the top of the comb near the grip and to do lots of final sanding all the way to 800 grit.
I used a rat tail rasp and then a length of electrical conduit with sandpaper wrapped around it to remove the wood for the flute.
Then the entire stock was then final sanded from 180 to 600 grit and the first application of tung oil was applied. 7 more applications to go.
After 7 coats of tung oil on the fore grip I gave it a rub down with 0000 steel wool and then thought I would embellish the underbelly a bit so I got out the gold metallic and black, oil based sharpie paint pens and had a go at it. A few more coats of tung oil over the top of the paint will seal it in real nice.
I took it outside and shot a very brief video of the finish so far.
Enders fore grip stock with tung oil finish - YouTube
I am almost to the point where I can check “making a gun stock” off the list of things I have always wanted to try doing.
When I tried to disassemble the metal parts of the rusty old gun I was unable to turn the three screws that hold major components. I was bending the tips of screwdrivers and at least one screw slot was showing damage from attempts to break it free. I didn’t want to apply heat to such an old weapon and sure as hell didn’t want to snap the head off the screws with an impact driver. What to do?.............. Google it.
Penetrating oil was the likely solution but in searching for the best performing product I came across a recipe I had not heard of but Im given to understand its no secret to mechanics and gun smiths.
It calls for equal parts Automatic transmission fluid and Acetone. Should you encounter corroded screws or bolts and find yourself in need of penetrating fluid I can highly recommend this concoction. I found this blurb online.
Machinist’s Workshop magazine tested penetrants for break out torque on rusted nuts.
They arranged a test of all the popular penetrants with the control being the torque required to remove the nut from a “scientifically rusted” environment.
Penetrating oil ….. Average "break free" load
None …………………........ 516 pounds
WD-40 ………………........ 238 pounds
PB Blaster …………........ 214 pounds
Liquid Wrench ……...... 127 pounds
Kano Kroil …………....…. 106 pounds
ATF-Acetone mix…....….53 pounds
.
The ATF-Acetone mix was a “home brew” mix of equal parts automatic transmission fluid and acetone.
Note the “home brew” was better than any commercial product at unseizing rusted fasteners and not just by a little. It really out performed any other product on the market.. Its much less expensive than specialty oils as well. A quart of ATF is less than $4 and a quart of acetone costs about $6.
I hoped to speed the penetrating action by submerging the entire receiver in the mixture and then vibrating it with an ultrasonic cleaner/bath. The only problem is, I don’t have an ultrasonic parts cleaner.
What I do have is an old Oster hair trimmer and an empty bean can.
If you are concerned about mixing the highly flammable Acetone fumes and electricity, you can run this device on your neighbor's patio while he is at work. (safety first). Here is a short video of this engineering marvel at work.
Transmission fluid and acetone and hair clipper - YouTube
I let the receiver soak in the solution for 24 hours then wiped the entire assembly dry. The seized screws and pins were removed with normal hand held screwdriver torque with no damage to the parts. The fluid had soaked the threads the entire depth of the parts. Im impressed by this simple mixture of fluids and will store that trick for future uses.
Now the shotgun is reduced to 40 rusty parts.
All the parts are bagged with labels telling me what they are for. I photographed every step of disassembly. I don’t want parts (some are very close in appearance to one another) to get mixed up. As I restore them they will be re-bagged until such time as I reassemble the shotgun.
Now the fun begins. I can replace nostrils full of powdered walnut with powdered iron and steel.
Im starting with the spring mechanism for the fore grip since the fore grip finish is nearly complete. This assembly is made up of 7 parts, all of which are pretty corroded. This assembly also spent time in the ATF and Acetone solution so I could take it apart.
Here it is right off the gun as I received it.
I screwed up here and failed to take a pic of the metal parts after cleaning and before bluing but here are the parts after bluing.
The S.O.P. for the parts is as follows.
- Disassemble
- Manually descale (Dremmel, sandpaper, files, steel wool, etc) to get rid of as much surface rust as possible
- Acetone bath with tooth brush (to degrease)
- Chemical rust remover (30 minutes or longer on really corroded parts)
- Water rinse and dry
- Manual rust removal of any spots missed
- 400 grit sanding, Steel wool and polish
- Acetone bath
- Dicropan cold bluing
- 0000 steel wool
- Acetone bath
- Dicropan cold bluing
- 0000 steel wool
- Acetone bath
- Dicropan cold bluing
- 0000 steel wool
- Light oil
- Bagged and tagged
The triple bluing and steel wool seems to give it good color and protection and shine.
All these parts are rusted and pitted so badly that it is not possible to remove all the pitting as it would dimensionaly change the parts or compromise them. While the pitting remains, the chemical rust remover does a good job of removing the rust and the small metal brush of the Dremmel gets into all the pits.
Many of these parts will need to be degreased again before I apply the baking lacquer ( protective coating) but for now they all get thrice blued and oiled.
Here is the fore grip spring mechanism reassembled after blue and oil. Not picture perfect but corrosion protected and functional. It will be disassembled again for the baking lacquer.
I did a better job with the pictures on the Trigger and trigger guard. Im not going to show all 40 pieces being restored as that would only slow down the whole process and there are a lot more parts to deal with but you get the idea. Its going to be a tedious process.
With all the small parts finished, I can move onto the receiver and barrel. I put naval jelly and the receiver in a gallon sized ziploc bag for 2 hours. Im impressed with its ability to remove all corrosion. Then it was the same regimen used on the small parts all the way up to polishing.
It cleaned up well but I did a lot of extra polishing work.
Here is a short video of how it looks just prior to cold bluing.
Enders Royal Western Receiver housing after rust removal - YouTube
Here it is after being cold blued 3 times.
The receiver will be coated with Brownells baking lacquer colored stainless steel grey to mimic the metallic look the gun had originally.
Then it was onto the barrel. Earlier in the process while I had the ATF and Acetone solution in use, I soaked the barrel in order to remove the attached parts. I also used the solution in the bore with a copper brush. What came out of the bore looked like crude oil. I worked that brush through the barrel many many times.
While working the receiver I soaked one end of the barrel in the naval jelly. My container was too large (or I didn’t have enough naval jelly) so I threw some wood strips in to raise the level of the jelly. After 2 hours I pulled it out and rinsed it under hot water and dried it and only gave it a brushing with a stiff stainless steel bristled brush and then steel wool to remove the powdery grey surface created by the naval jelly.
The effects are pretty noticeable. Here is a video showing how well it worked.
Enders Royal Western barrel rust removal - YouTube
After 6 years, (and lots of projects) my Dremmel tool died. Off to the store for another.
While I was out buying another Dremmel tool I picked up two more containers of naval jelly so I could remove the rust from the entire barrel. I cut in half a plastic tube that paper comes on for our plotter at work. This tube bathtub worked pretty well once I plugged the ends with foam and tywraps.
After 2 hours I pulled it out and rinsed it under hot water and dried it. Here it is with the powdery grey film left by the naval jelly.
Then the wire brush and steel wool treatment.
After 3 applications of Dicropan cold blue.
The next step is applying the Brownells baking lacquer. I did most of the baking lacquer parts in the shop oven. If you haven’t tried this stuff yet, it great. Ive done other guns with it. It easy to use and durable. Certain parts (in keeping with the original look of the shotgun) would be black while others would have a metallic appearance. I preheated the oven to 300 and got to spraying the parts with 3 light coats. Here they are baking for ½ hour.
The 30 inch barrel of course would not fit in my oven so I had to improvise and build at tall skinny oven just for the barrel. I used an electric hot plate, some stove pipe, plywood, tin foil, and a wire hanger.
I let that engineering marvel preheat while I took a diamond tool mounted in my Dremmel to the barrel to add a marking that was missing.
The barrel also cooked for 30 minutes.
Here are some of the small parts after they cooled and after I ran a tap through all the holes to clean up the threads from the over spray.
Here is the barrel after its cooled and two applications of paste wax applied.
I am ready to begin assembling all the parts into a gun. Im making progress on the butt stock as well. After several coats during this week, I took after it with 600 grit sandpaper and gave it another of many applications of tung oil.
When I began this project I took dozens upon dozens of photos during the disassembly process to aid me in reassembling the gun since I knew there was going to be a good deal of time before I would be putting the pieces back together and I wouldnt remember how to do it. I took pictures of the parts in their assembled state to see how they interfaced with one another like this.
Then as I removed the parts I took pictures of the orientation so I could reverse the process later on like this.
Despite my best efforts I still managed to mess up the reassembly. On more than one occasion I failed to pay close enough attention to my photos and tried to put it back together incorrectly. Perhaps I was in too great a hurry. Once I slowed down and really studied the pictures and put things back not only in the proper orientation but in the right sequence (some parts had to be assembled before others) then it all came together quite well. At this point all the metal parts are reassembled. Here are a few before and after pics.
These two springs proved to be the most difficult to compress and reassemble. I can envision the custom tool they no doubt used in mass production. I spent the most time coming up with a way to reinstall these springs without marring the finish on the receiver.
Before
After
Before
After
Before/After
Before/After
Then I turned to the fore grip wood and spring assembly. There are still more applications of tung oil to be worked into the butt stock so I can't assemble the complete shotgun so I will turn my attention to building a remote means of test firing this old gun. I need to make a sled to hold the gun securely and a way to trigger it from about 60 feet away. Back to making sawdust
Down to the final 2 applications of tung oil on the butt stock so I am prepping the test firing sled.
The gun will be secure in foam and I can pull the trigger from 60 feet away while the video camera captures it all up close
The gun rehabilitation is complete. The stock is finished. Here it is sitting on what remains of the walnut beam if came from.
Here is a brief video that better shows the stock finish.
Enders Royal western stock finished - YouTube
The 2 ½ inch 16 ga shells arrived in the mail today. All I need is the weather to improve so I can test fire it. At any rate, here it is in its completed state.
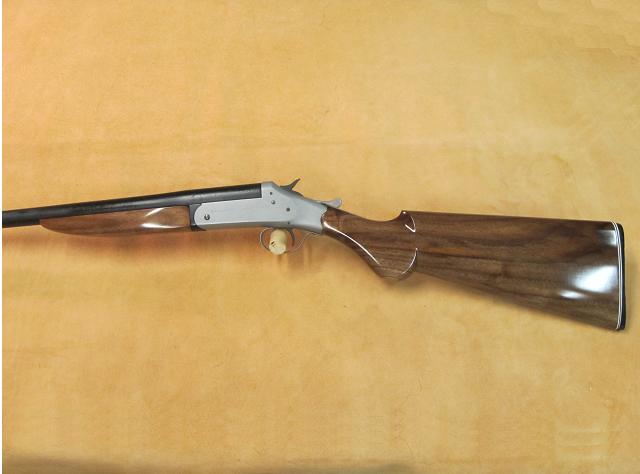
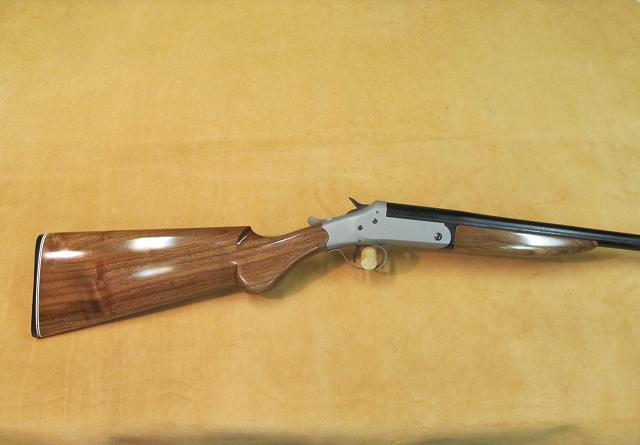
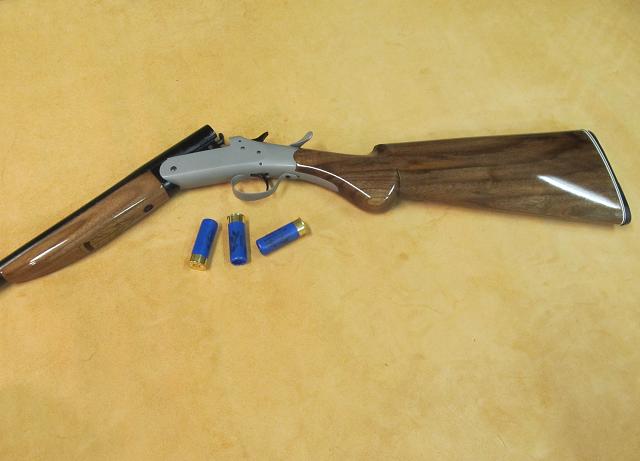
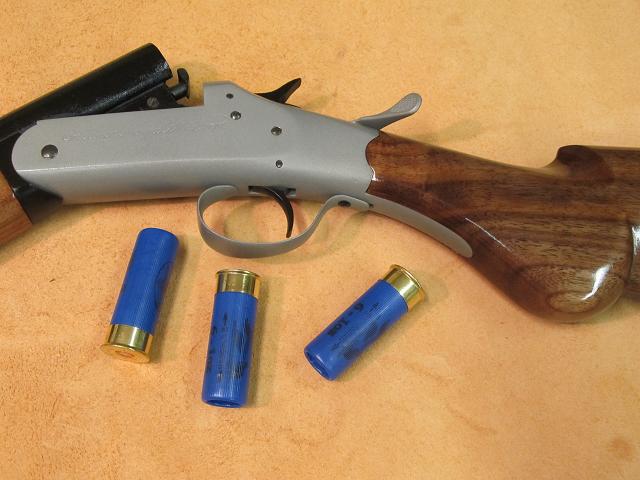
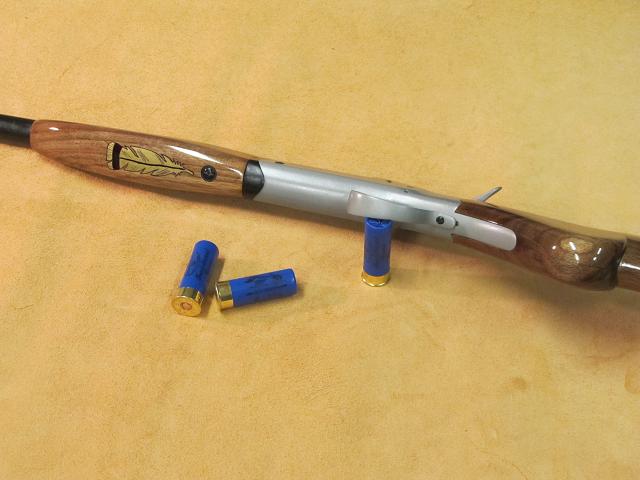
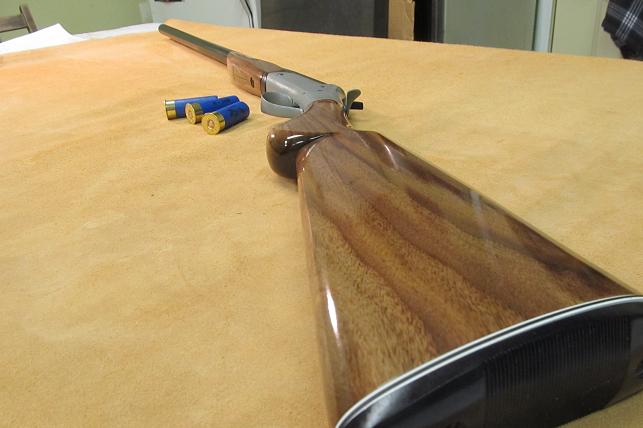
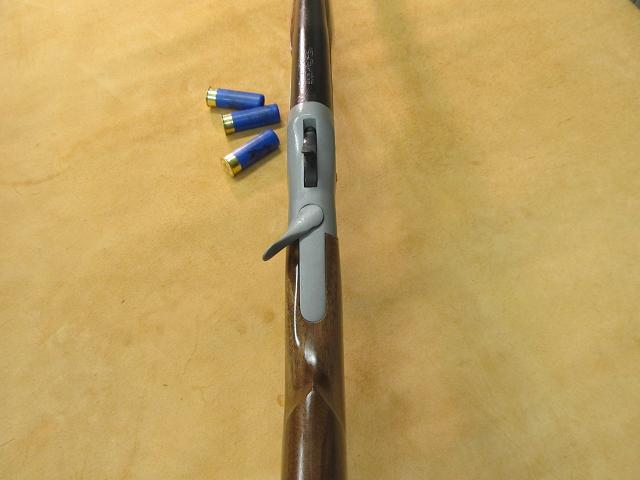